The selection of materials is one of several critical steps in the aircraft design process. Aurora’s Materials, Processes, and Testing (MP&T) engineering team does the work to define material requirements for a given design and then determine the optimal materials and process conditions for transforming those materials into aircraft components that exhibit the required properties. Given Aurora’s place at the cutting edge of aircraft technology, our MP&T team is frequently working on rapid prototyping and testing of novel material applications and manufacturing methods.
Experimental aircraft programs, where we build a unique aircraft for the purpose of demonstrating and testing new technologies, offer the opportunity to explore materials and processes that are not commonly used in the aerospace industry. One example is metal 3D printing, which was used to create a complex aircraft part with geometry that was difficult to fabricate using conventional manufacturing processes. Because metal 3D-printed parts are uncommon in aerospace, the tests to assess their compliance with requirements are also unique. Aurora’s MP&T team developed and implemented tests and fracture analyses methods to understand the failure modes of the part and confirm that material properties of the metal 3D-printed part matched the design.
Composite materials, and particularly carbon fiber composites, are common in aerospace applications, but Aurora MP&T experiments with uncommon manufacturing methods for composite parts. Two examples of this work are adhesive bonding and resin infusion, which offer opportunities to reduce cost and weight. The aircraft wing spar, the main structural member of the wing, is another example. Aurora designs and prototypes composite wing spars of non-conventional cross sections and fiber orientations in order to optimize the delicate tradeoff between weight and strength.
In each case of novel materials or processes, rapid prototyping allows the team to quickly prove out techniques on a practical scale early in the design process. Aurora uses a variety of prototyping techniques including hand layup, resin infusion, automated fiber placement (AFP), and 3D printing.
“Our philosophy is to quickly build something to demonstrate and test,” said Kevin Razon, MP&T group manager at Aurora. “Taking an idea from paper to a tangible test article is how we prove out new ideas on a timeline that aligns with our fast-paced aircraft development programs.”
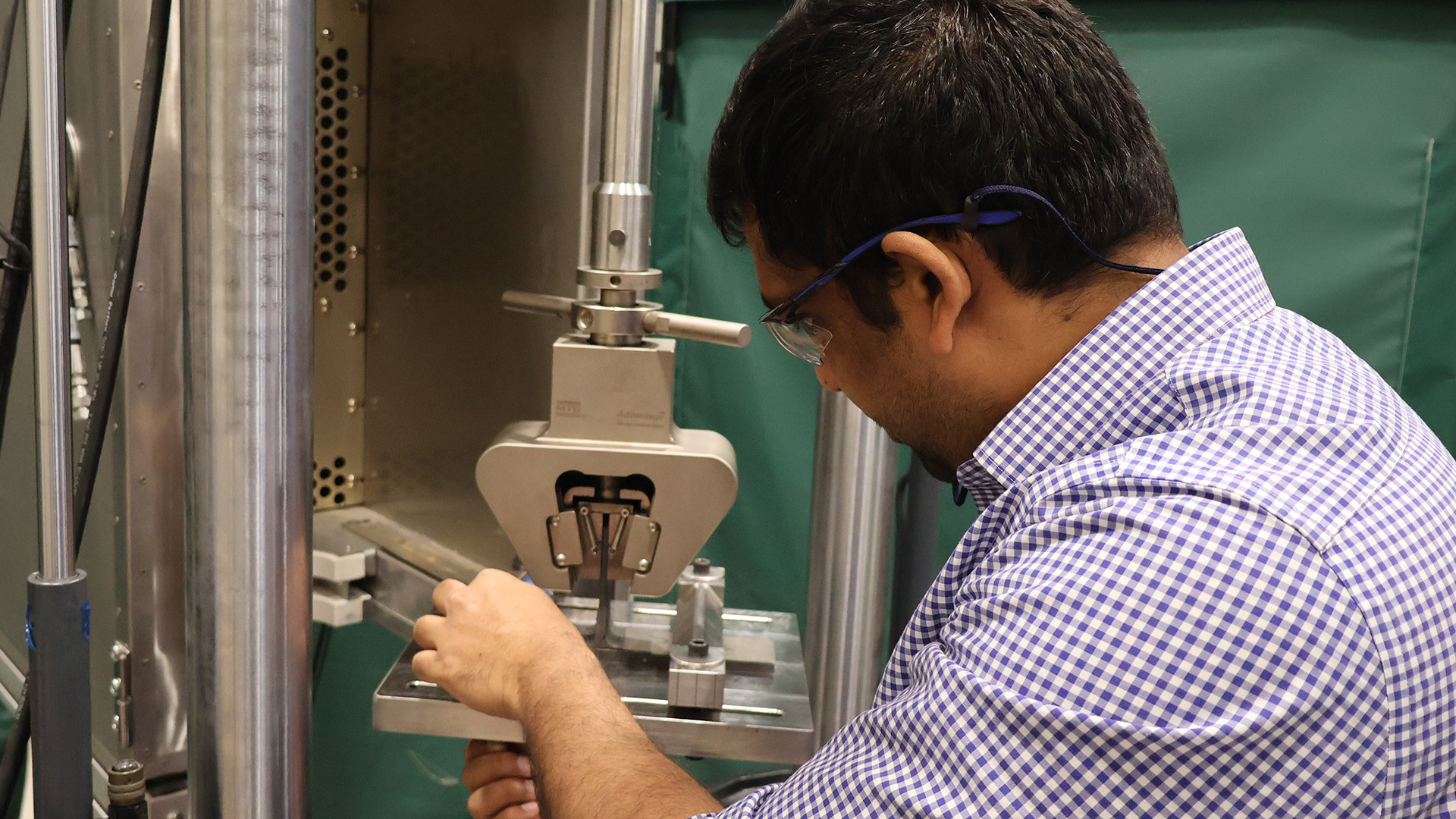
To test the compliance of unique manufacturing processes and designs, the MP&T team uses both standard and customized testing. One example is the universal testing machine used to test mechanical properties such as tensile, compressive, and flexural strength. The machine is fitted with either industry standard or Aurora-designed tools to conduct the needed tests on a specific part. Since aircraft operate in different environments, many material tests are conducted inside a thermal chamber at temperatures as low as -65ºF and as high as 180ºF.
Other tests characterize the electromagnetic, thermal, and chemical properties of the part. The team also examines composite materials at up to 200x magnification to measure minute details such as tiny pores and the diameter of individual carbon fibers. This helps Aurora to thoroughly understand an aircraft structure at the microscopic level. We also apply the information to set standards for the non-destructive testing commonly used in Aurora’s regular production aircraft programs.
“The number of variables that we can design and test for can sometimes seem unending,” said Razon. “But when we find the ‘just right’ combination of materials and processes, we can deliver solutions that enable aircraft to achieve something that has never been done before.”